Filling, Purging & Pressurizing your System
Properly filling, purging, and pressurizing a hydronic radiant heating system is essential for efficiency, longevity, and performance. Eliminating air pockets prevents uneven heating, noisy operation, and reduced efficiency, ensuring smooth heat transfer. It also prevents pump cavitation, which can damage the pump and shorten its lifespan. By removing trapped air, the system maintains even heat distribution, preventing cold spots and ensuring consistent comfort. Correct pressurization is crucial for smooth operation, preventing issues like low flow, overheating, or unnecessary stress on components. Additionally, a well-maintained system reduces wear and tear, minimizing the risk of leaks, corrosion, or premature failure. With proper filling, purging, and pressurization, the system operates at peak efficiency, lowering energy consumption and reducing heating costs. Routine maintenance is key to keeping a hydronic radiant heating system reliable, efficient, and long-lasting.

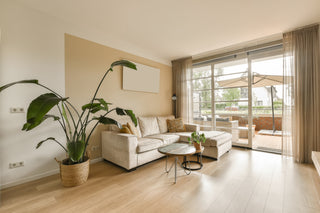
Fill / Purge / Pressurize Your System
After everything is installed and connected, it is time to introduce fluids into the system and purge the air out of the system.
What You Will Need:
*Note: 100 feet of 1/2" Tubing will require approx. 1 gallon of fluids
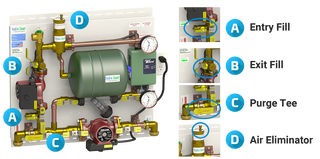
System Overview
PANEL DETAILS
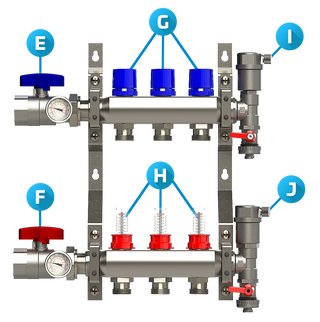
MANIFOLD DETAILS
BEFORE FILLING THE SYSTEM
ON THE SYSTEM

1. Connect Hoses to the System
• Attach Hose 1 to the OUT on the TRANSFER PUMP and connect to ENTRY FILL (A)
• Attach Hose 2 to the IN on the transfer pump and run into the bucket
• Attach Hose 3 to the EXIT FILL (B) and run into the bucket
• Fill 5 gallon bucket with Distilled Water/Propylene Glycol
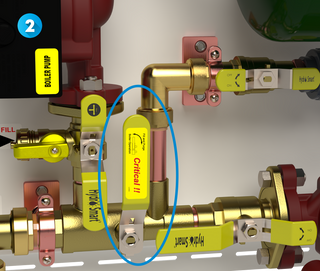
2. Make sure the PURGE TEE (C) is in the vertical position
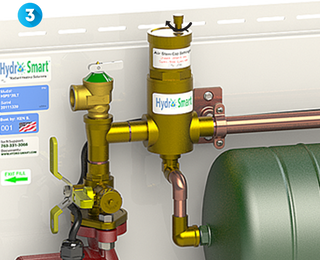
3. Close AIR ELIMINATOR (D) by turning air stem cap clockwise
ON THE MANIFOLD
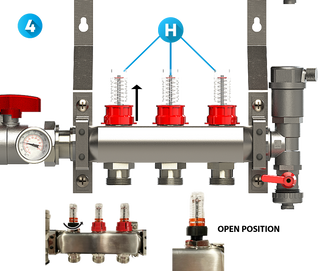
4. Verify all FLOW METERS (RED/H) are fully OPEN
(Pry locking ring up and turn CCW until fully open then push down locking ring to lock into position)
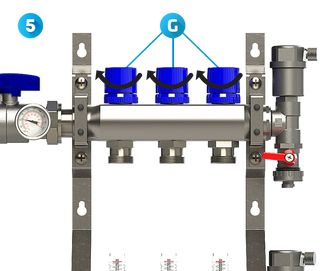
5. Verify all LOOPS (BLUE/G) are CLOSED on the manifold by turning CW
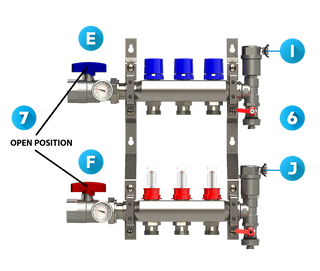
6. Verify Air Eliminator Valves
(I & J) are CLOSED (CW)
7. Verify Return and Supply Shutoff Ball Valves
(E & F) are in the OPEN position
FILLING THE SYSTEM
PURGING
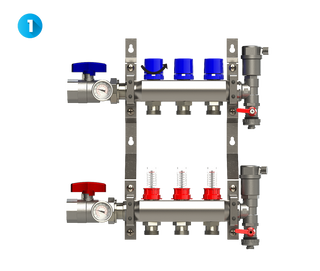
1. OPEN the FIRST LOOP* by turning Blue Cap Counter Clockwise (CCW) then turn on TRANSFER PUMP
NOTE: Each loop will take approx. 2-3 minutes to purge. *The number of loops will depend on your system.
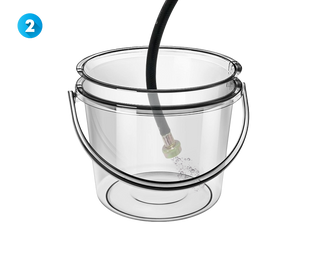
2. Observe air bubbles in the bucket dissipating for removal of air.
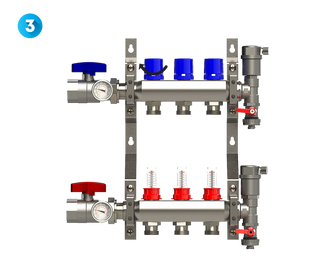
3. When air is purged out, CLOSE LOOP by turning Clockwise (CW)
Repeat steps 1 - 3 with each remaining loop until all loops have been purged
PRESSURIZING
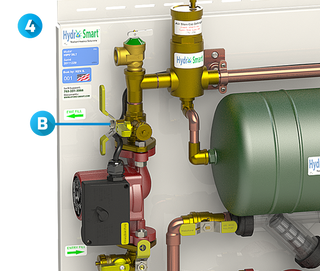
4. With the transfer pump still running, CLOSE off FILL EXIT POINT (B) valve and the pressure will rise.
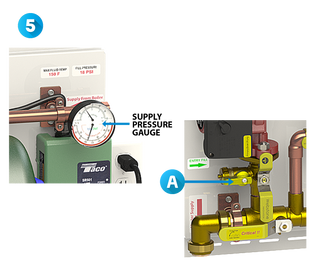
5. When supply pressure gauge shows 16-22 PSI, CLOSE OFF FILL ENTRY POINT (A)
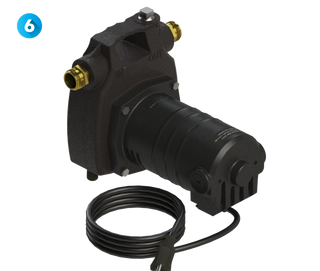
3. Turn off transfer pump and remove hoses.
YOUR SYSTEM IS NOW PURGED AND PRESSURIZED!
BEFORE BOILER OPERATION
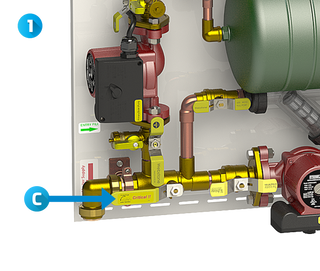
1. Rotate PURGE TEE (C) to horizontal position
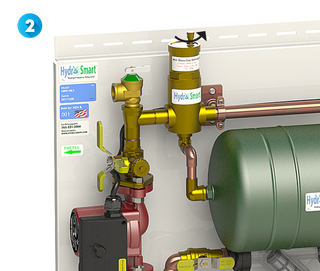
2. Rotate AIR ELIMINATOR (E) stem cap screw counter clockwise 1 turn